Summary
A pharmaceutical company looking to utilize our automation services to deliver a vaccine to broiler chicken eggs has become one of the longest-running clients in company history. Over 30 years ago, our engineering and assembly teams assisted in the development of a patented automation system to inject eggs with a vaccine prior to chicks hatching. This solution is a more humane way to ensure disease-free chickens, is mobile to move down the aisles in a hatchery to inoculate a quantity of eggs at once, and we replicated the system to be distributed into countries across the globe.
Challenge
Develop a portable machine to inject a vaccine into chicken eggs prior to hatching, and install these systems in hatcheries all over the world.
Insights
In 1989 Fred Rexon Jr. (then-sales engineer, and current President/CEO) received a call from the engineering manager at a startup pharmaceutical company in North Carolina, looking to develop a machine to inject a vaccine into live broiler eggs. This company had been working on a prototype for some years, and the previous method involved inoculation into individual newly hatched chicks. This method proved to be very costly, so they sought a more automated process.
Trays of eggs would be incubated for 18 days, and three days later the chicks would hatch. The company’s target was to inject the eggs on the transfer day between the incubator and hatcher. A key factor was for the system to be built on casters, allowing it to move easily down the multiple aisles of chicken hatcheries. Our team agreed to develop this mobile system along with the controls of each step of the process, turnkey as one unit.
A year after the initial call, Precision Automation® built the first prototype system and it was installed for beta testing, machine refinement, and finally: acceptance. Precision signed an agreement to be the exclusive manufacturer of this system, as our sales engineering team understood the market for this type of system and recognized the potential for significant growth.
The first system was financed in a way that our company accepted most of the costs, justifying the decision with future business in mind, and a guarantee of keeping our machine shop busy with an influx of steady work. “Our engineering and manufacturing capabilities made us an ideal partner for [the customer] to move forward with this project” states Fred Rexon, the initial lead project manager.
One of the reasons why this client chose us to design and develop this system was our extensive experience with various pharmaceutical applications. They also appreciated the many stainless-steel applications in our repertoire, which showed our capability to manufacture the exact type of equipment they sought. That material construction allowed each system to be 100% washdown capable, allowing the customer to clean the systems after each production run. In addition, the solution was designed such that every punch/needle is cleaned and sanitized after each injection.
Our Director of Manufacturing at that time Dave O’Reilly spent years overseeing all aspects of this project, dealing with the customer directly: both their Purchasing & Engineering departments. Numerous shop employees at Precision Automation® participated in discovering better ways for the system to be assembled, which shows our company’s commitment to continual improvement.
Dave was instrumental in facilitating the flow of our shop when it came to this project, constantly looking for ways to get processes completed faster. Additionally, all members of our engineering department looked out for inconsistencies & took an analytical approach at each of the numerous drawings. These actions saved time & money, and those benefits were shared with the client.
The Precision Automation® team has refined our process of Order > Release > Purchase > Ship which is now extremely efficient with this project. For instance: what traditionally took 16 weeks when the project began, now takes less than 12. The assembly process has become almost second nature for our employees who have gotten to know many of the tricks and intricacies of the system.
With a wide variety of end-user customer locations in various states domestically, as well as plenty of countries on all different continents, our team had established multiple system editions to work with their respective locations, and each one’s specific requirements. Precision arranged to send representatives to several locations to investigate testing procedures so we could emulate their process and complete these procedures in our shop on the front end, prior to shipment. Our challenge was to validate all the operation, maintenance, and cleaning processes prior to shipment, to ensure fast and easy plug & play of each system when they reached their final destination hatchery.
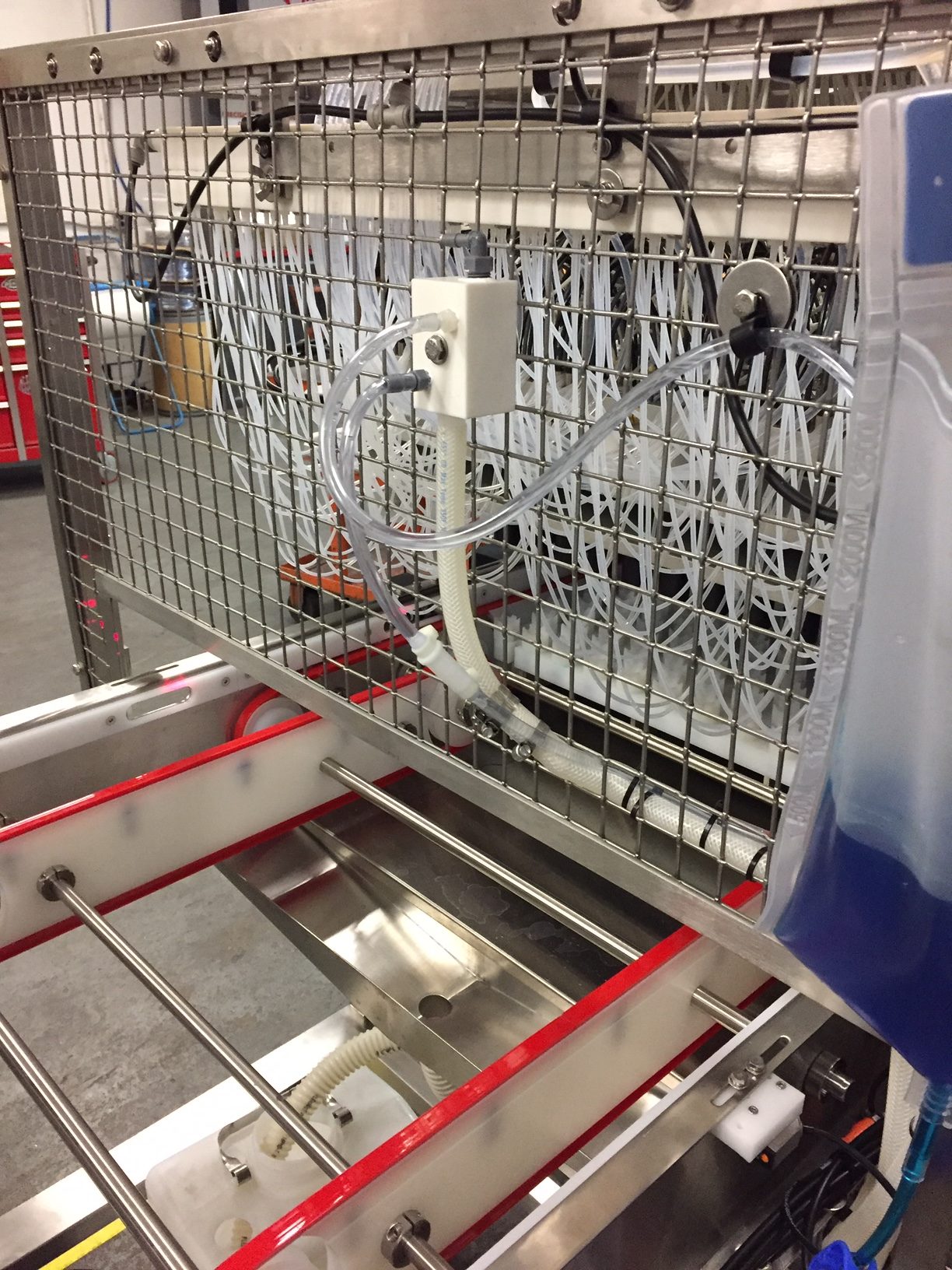
- Humane Chicken Egg Vaccines
- Turnkey Solution from A to Z
- Mobile System Built in Quantity
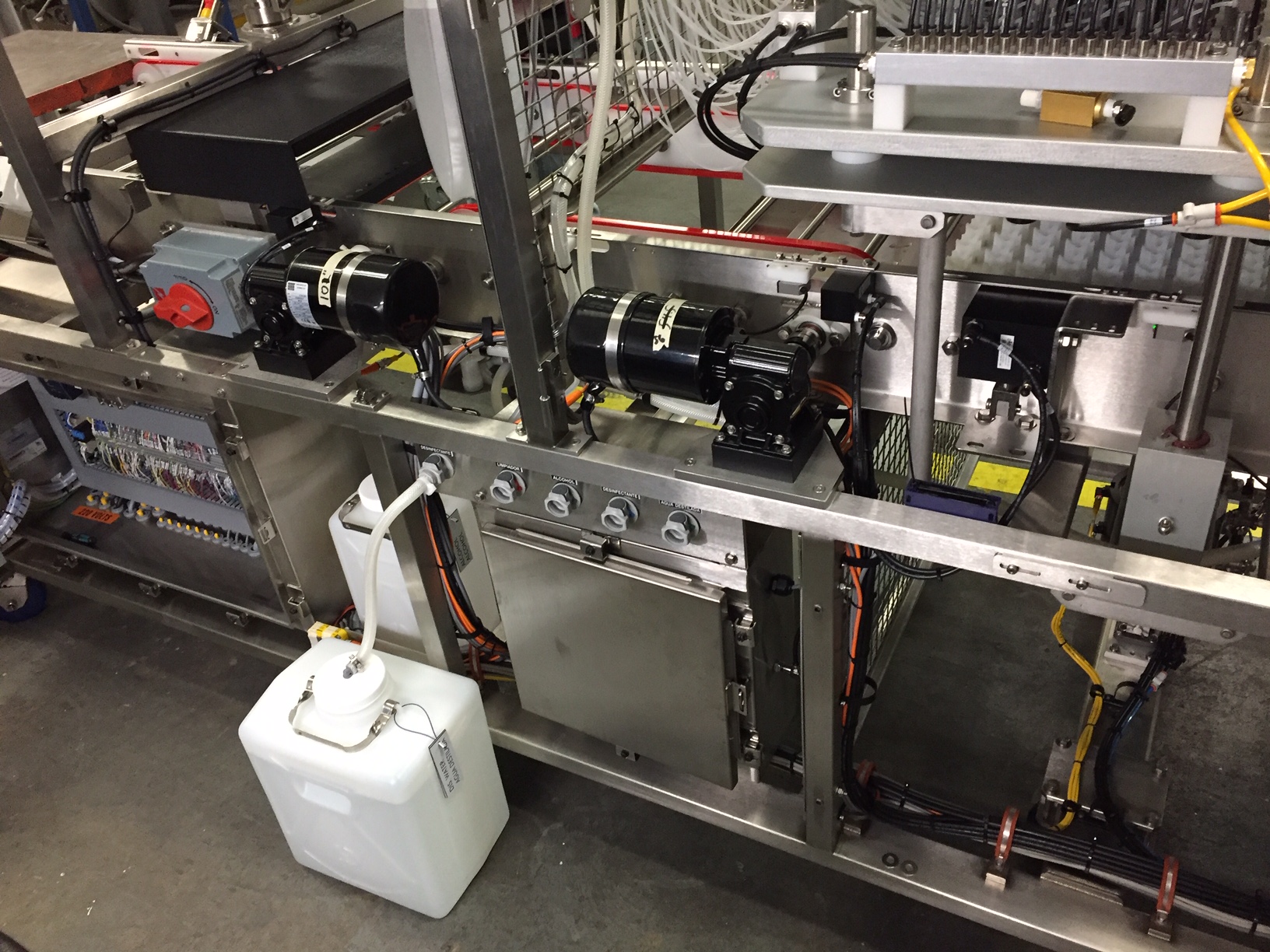
Conclusion
This project has eclipsed over three decades, and our team has had countless employees working together to produce systems for this customer. Our company’s experience in the pharmaceutical industry as well as our overall shop capabilities allowed us to be a perfect match for this customer. Through revisions and continual improvements, the Precision Automation® team has significantly enhanced the machine proficiency with over 2,000 vaccine inoculation systems, egg transfers, and egg removers.
The impact of this project is understood through the vaccination of the countless number of eggs that go on to hatch into chickens. As our Executive VP/COO Gerry Renzi states: “Approximately 98% of the chicken that you have eaten has gone through one of these systems.” Our shop has demonstrated the ability to create a mobile, bulk-vaccine delivery system that answers the client’s initial requirements as well as minor modifications in order to maximize efficiency and provide safe chickens for human consumption.