Summary
This project involved integrating labeling machinery, conveyors, and vision systems at 20 locations across the United States, Mexico and Canada. Over the course of two and a half years, Precision Automation® installed over 100 complete Labeling Systems throughout North America, with accompanying material handling and Vision Inspection Systems that verified the label was applied to the case. Our team ensured future success in these systems by providing comprehensive on-site training for employees to fully grasp the capability of our equipment.
Challenge
Integrate Labeling Machinery, conveyors, and vision systems on a large, multi-national scale that included 20 facilities and 100 packaging lines across North America, each line with varying configurations and needs.
Insights
Previous to Precision Automation®’s intervention, this customer was forced to purchase pre-printed corrugated display cases for each season/holiday AND for the candy product therein. Given the number of options that one corrugated case could hold, there were hundreds of SKU combinations to purchase and inventory. For example, the design of the corrugated display case for Valentine’s Day might include images of hearts, cupid and roses. However, with dozens of combinations of content options, the customer needed to have various Valentine’s cases with other numerous identifiers of the contents (such as chocolate, chocolate with almonds, peppermint candy, caramel, etc.) These combinations multiplied by dozens of seasons/holiday options yielded hundreds of different cases they needed to purchase. Furthermore, minimum order quantities added strain to the already demanding purchasing requirement and inventory management process.
The idea of the project was to consolidate the large number of corrugated display cases down to only those that that represent seasons or holidays. The customer would leave an unprinted area on the box where a pressure-sensitive label would be the unique identifier of the contents.
Pressure-sensitive labels can be manufactured efficiently, with thousands of labels on a single 15-16” diameter roll. This enables the customer to purchase fewer corrugated display case options and many different SKU’s of labels, which are much cheaper and often don’t require massive minimum purchase quantities. The customer would immediately gain tremendous flexibility in purchasing and inventory management, while also saving a considerable amount of money on the consumable cost factors.
Precision Automation® proposed a solution that included Arca Labeling Machinery (specifically the Evolution 160, Arca’s workhorse Label Applicator), Keyence Vision Inspection Systems, and custom fabricated Support Stands. Our team’s expertise in integration, controls, and fabrication proved a major benefit throughout the project. The customer would often require a modified stand or different configuration for the vision system to meet each facility’s unique needs. Our collective flexibility and experience delivered effective results.
The project required effective communication and supply chain management, given that there were three major suppliers involved. Communication with the customer was paramount as well; there was a demanding installation schedule that required weeks at a time in numerous facilities scattered throughout Mexico, Canada, and numerous U.S. states- each location with a different point of contact and unique packaging line setup and requirements.
In some of the customer locations, production lines had been in place for years, thus integrating a new labeler and vision system within the middle of an established line called for some creativity. Teamwork between our technicians & project managers and the customer helped solve each case individually. Often the challenge was squeezing the equipment into a tight space, or re-wiring the interlocks with existing production line controls.
Our service technician team’s ability to travel to each of the respective locations for installation, training, and startup support was crucial to the project’s success. We were able to provide complete service and support for the newly installed systems, as well as comprehensive training for all operations employees at the beginning or ends of their shifts.
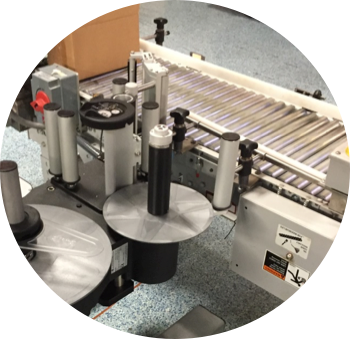
- Reduced Packaging Material
- Simplified Product Changeover
- Comprehensive On-Site Training
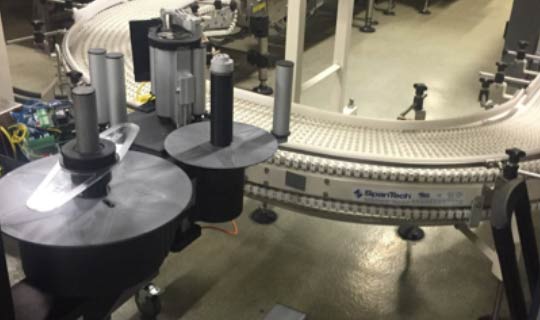
Conclusion
The successful completion of this project resulted in the customer greatly reducing the amount of packaging material, and the pressure sensitive labels becoming the unique identifier of the contents of each corrugated display case. The customer saved money by not having to order as many box SKU’s, and saved time by no longer having to organize and inventory them. Product changeover is also simplified, which smooths out the packaging operation at each of the customer’s 20 locations.
The project also allowed us to provide additional labeling opportunities in follow-on projects that were unrelated to the overall scope, which communicated to us that the equipment was working to their satisfaction and a good relationship had been established and maintained with this customer.