Summary
One of our valued recurring customers is a pharmaceutical diagnostic company who produces test kits. Within recent years they have required a significant increase in production capabilities. Their products diagnose a wide range of ailments including, most recently, SARS-CoV-2 (Covid-19). To meet demand and manufacture a significantly increased number of test kits, this company needed custom engineered systems to: handle the components, very precisely apply an RFID label, code, inspect, and verify the RFID label, reject noncompliant products, apply additional identification and protective labels, and release a finished product for packaging downstream. Our team navigated the user requirements and engineered solutions to ensure smooth and consistent operation, then meticulously tested each facet of these systems to confirm their amplified production rates.
Challenge
Develop highly precise, custom systems for product handling, labeling, RFID coding, and verification of differing cartridge-like products.
Insights
Our customer is a leading international pharmaceutical and diagnostics manufacturer with whom we have worked on multiple applications. The sales, engineering, and project management teams at Precision Automation® had already combined forces on previous projects where an automation system was specifically designed to maximize this customer’s efficiency. Sometimes the systems featured a rotary dial with custom fixturing, other times it transported products along continuously moving or precision indexing conveyors. Various machine platforms for differing products and requirements had been developed over the last decade. But each one of these unique systems had the same basic functionality of conveyance, labeling, coding, inspection, and rejection of nonconforming products.
What amplifies the complexity for these systems is the inspection & verification at each step of the process.
Our customer first required the confirmation of proper orientation on the infeed conveyor. Once the products are properly oriented, they are transferred into custom fixtures on a precision rotary dial. While on the dial, a labeling system applies a RFID label to the product. After application is complete, the product is indexed to the next station where inspection & verification ensures that the label was placed smoothly and precisely, within the small window of tolerance (+/- 1mm). Any product that fails inspection will be rejected.
After the RFID label presence and placement accuracy is verified, the RFID writing occurs. In this step, highly specific data (provided by the customer’s ERP System) is inscribed onto the label. The next inspection step then begins, to check and ensure that the data is readable. Soon after, while the rotary dial is indexing to the next station, a protective label is applied overtop of the RFID label. Once the overlabel is applied, it is also verified for presence and accurate placement.
Up to this point, the only information being applied is through RFID; none of which can be interpreted with the human eye. So next, a human-readable label is applied, which contains unique variable data such as date and lot codes. Once this human-readable label is applied, it is of course verified- this time through a process called optical character recognition (OCR) vision, to confirm the freshly printed codes are discernible to the human eye. Finally, the product is transferred off the Custom RFID Labeling System’s exit conveyor for further downstream processing and/or packaging.
The key to making this project successful was communication between Precision Automation® and the customer. Initially, our sales and project management team worked with the customer to develop a project specification. Subsequent RFQs were accompanied by a user requirement specification (URS) that specifically detailed system requirements. What began as a collaboration for a developmental and highly customized system set the expectations for future systems.
Through weekly meetings both in person and virtually, numerous changes and adjustments had to be made to adhere to our customer’s requirements, which often changed due to feedback from different departments. Precision Automation® had to be flexible in addressing new concerns and requirements as they arose. Our ability to adapt during a developmental process was integral to the success of this project.
In the end, our customer has expressed satisfaction with their completed automation solutions. A Custom RFID Labeling System, completely designed controls package, full fabrication, assembly, and testing at our facility was finalized and approved during comprehensive acceptance testing and installed soon after.
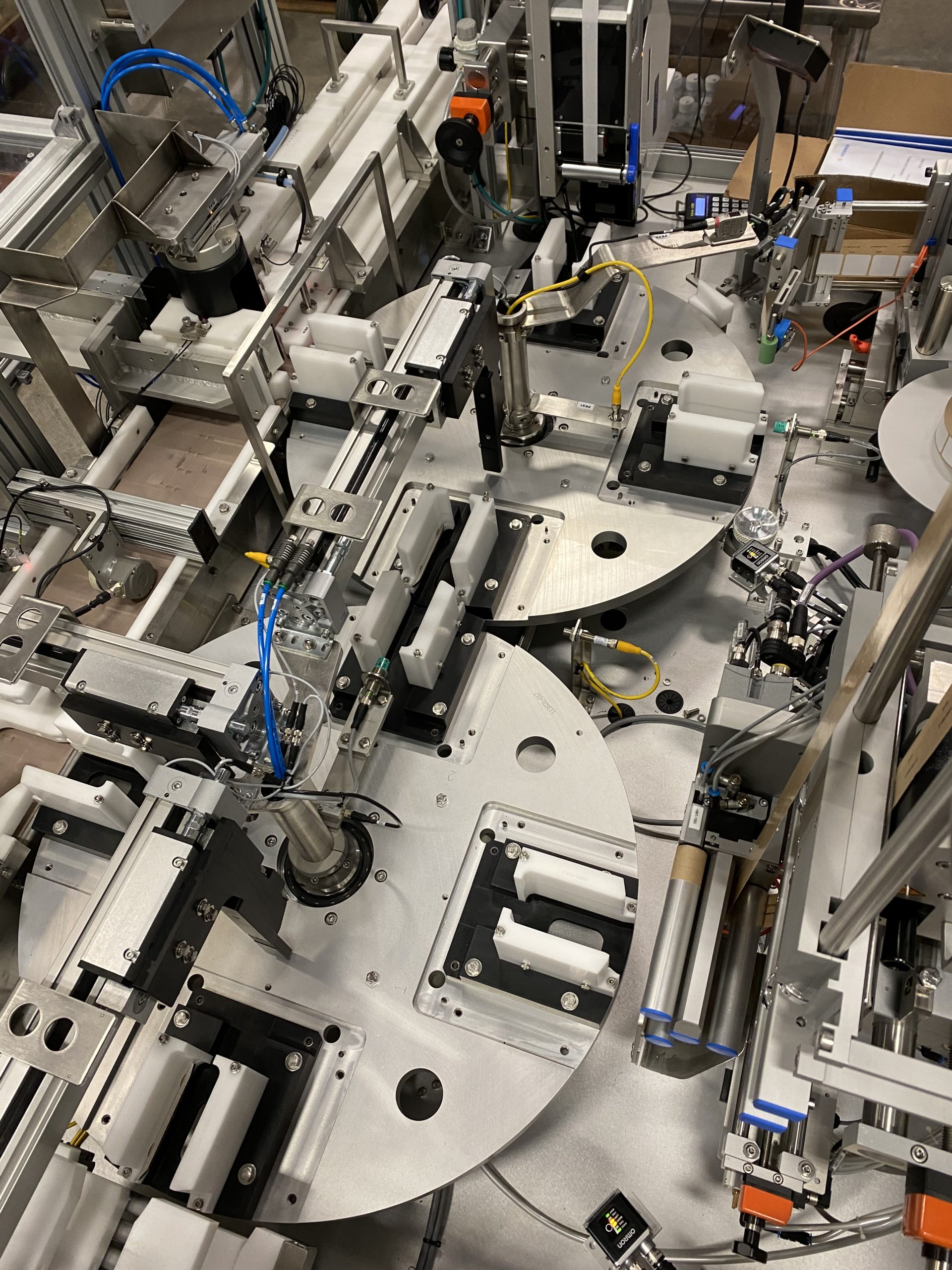
- Custom Engineered Equipment
- Tight tolerances
- Inspection & Verification at each step
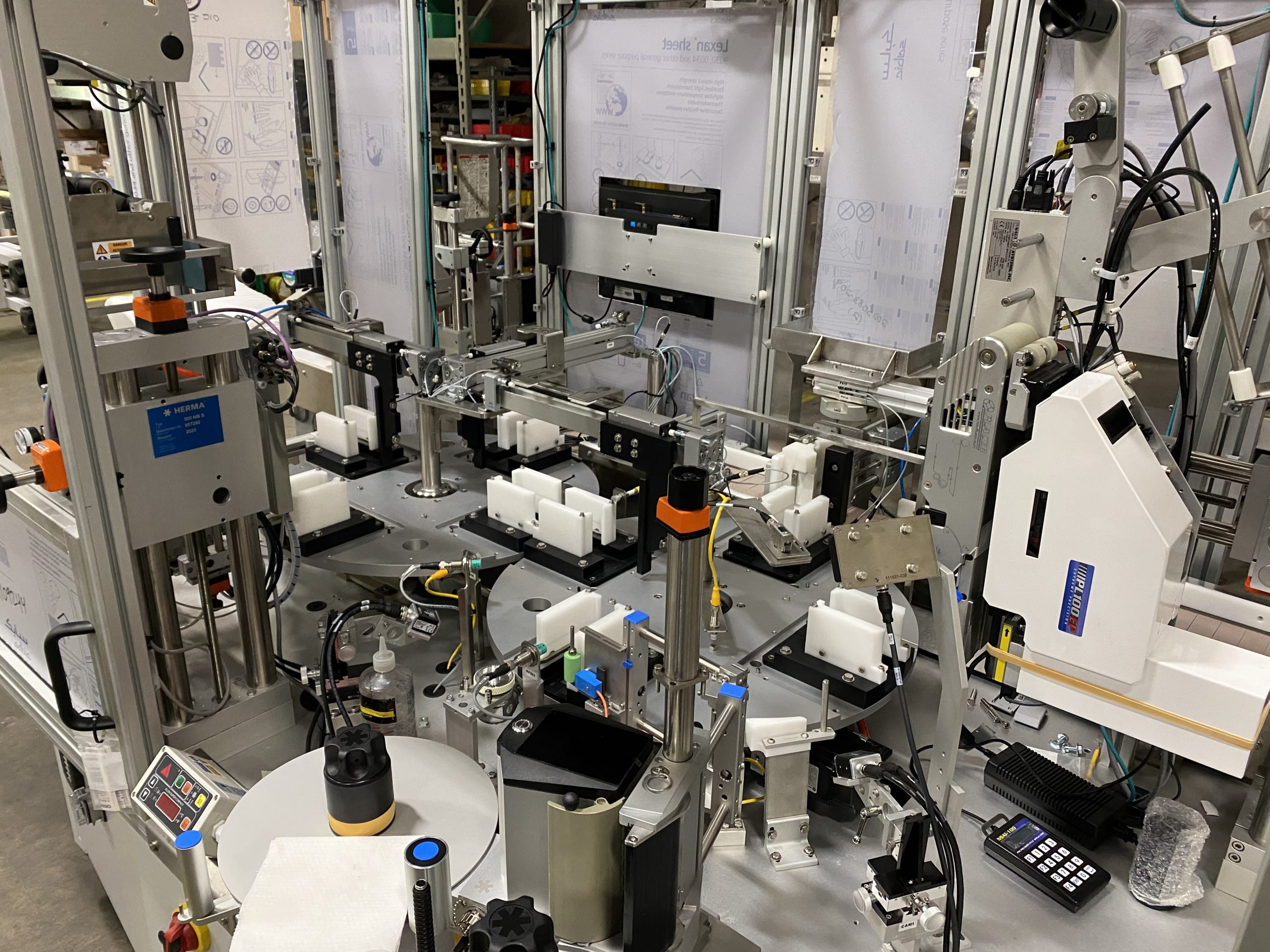
Conclusion
The successful design and implementation of this system platform has allowed for our customer to significantly increase the production volume of test kits.
In the years following the initial system’s development in 2010-11, Precision Automation® has provided several variations of equipment to accommodate numerous products. Some systems have been duplicated multiple times, incorporating technological and process improvements along the way. “Similar but different” RFID Labeling System platforms have been developed and provided, based on the differing requirements of a growing and changing product line. Additionally, many ancillary product handling, conveying, assembly, and packaging systems associated with these test kit products have been developed or are currently being developed.
The repeat business and additional opportunities serve as a testament to our customer’s satisfaction with the equipment provided and offer a basis to continue serving their needs in 2021 and beyond!