Summary
Simmons Pet Food is a manufacturer whose facility for wet pet food production in nearby Pennsauken, NJ recently increased their production capabilities. They had heard about some previous jobs completed by the material handling experts at Precision Automation® within the pet food industry and contacted us for assistance. Our task was to integrate multiple production lines- producing varying sizes of pet food cans- into a single packing & palletizing process, which would ultimately yield smaller packs of pet food at higher speeds.
Challenge
Design a layout (utilizing a limited amount of space), manage the influx of equipment need to complete the packaging line, and install a turnkey system to increase their manufacturing speed and efficiency.
Insights
Simmons Pet Food is a leading North American private-label and contract manufacturer of wet and dry pet food and treats. Proudly sourcing high-quality ingredients, Simmons produces premium and value-focused pet food for the best brands in the industry. The production line that we were tasked with handles cans of wet pet food at high speeds, and at varying sizes: 5.5 oz., 13 oz., and 22 oz. These cans are packed together and shrink-wrapped into trays, and then stacked into pallet loads.
In order to move these individual small product cans at high speeds, our team arranged to source various pieces of equipment while still maintaining the fork lift aisles and walkways for Simmons employees. The key part of the project was the integration of multiple lines that fed into two separate (existing) labeling machines, as well as two existing packers- plus an additional packer that we supplied. This would increase the flexibility for Simmons’ operators to choose the optimum line on a given shift/day.
Perpetual Merge Conveyor Video
The complete solution was designed so that one production line will handle the 5.5 oz. cans and 22 oz. cans, which will be packed, labeled, and palletized; while the other production line will handle, pack, label, and palletize the 13 oz. cans. The cans move down the line at approximately 70-80 packs per minute, and our team used ceiling-hung conveyor to maximize the space allotted for the system. The video above depicts a unique perpetual merge conveyor we implemented to unite two lanes of packed product into one.
After the final designs, installations, and corrections were complete, Simmons had gained a new complete system in the form of: a packer, a perpetual merge, over 500 feet of conveyor from four different manufacturers, a palletizer, and multiple crossovers (to allow foot traffic to access the full floor space).
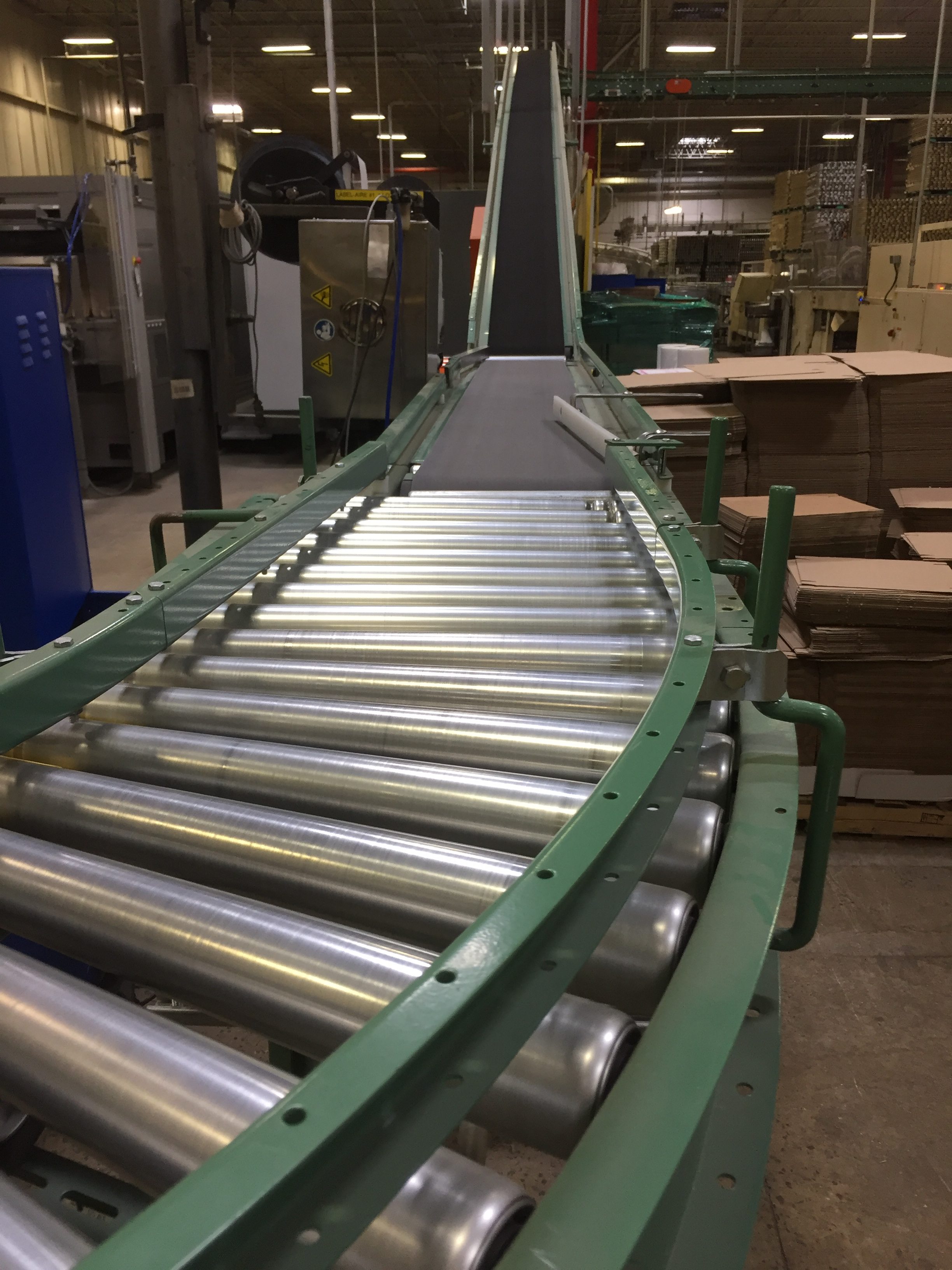
- Increased Amount of Flexibility
- High Speed Material Handling
- Conveyor and Machinery Integration
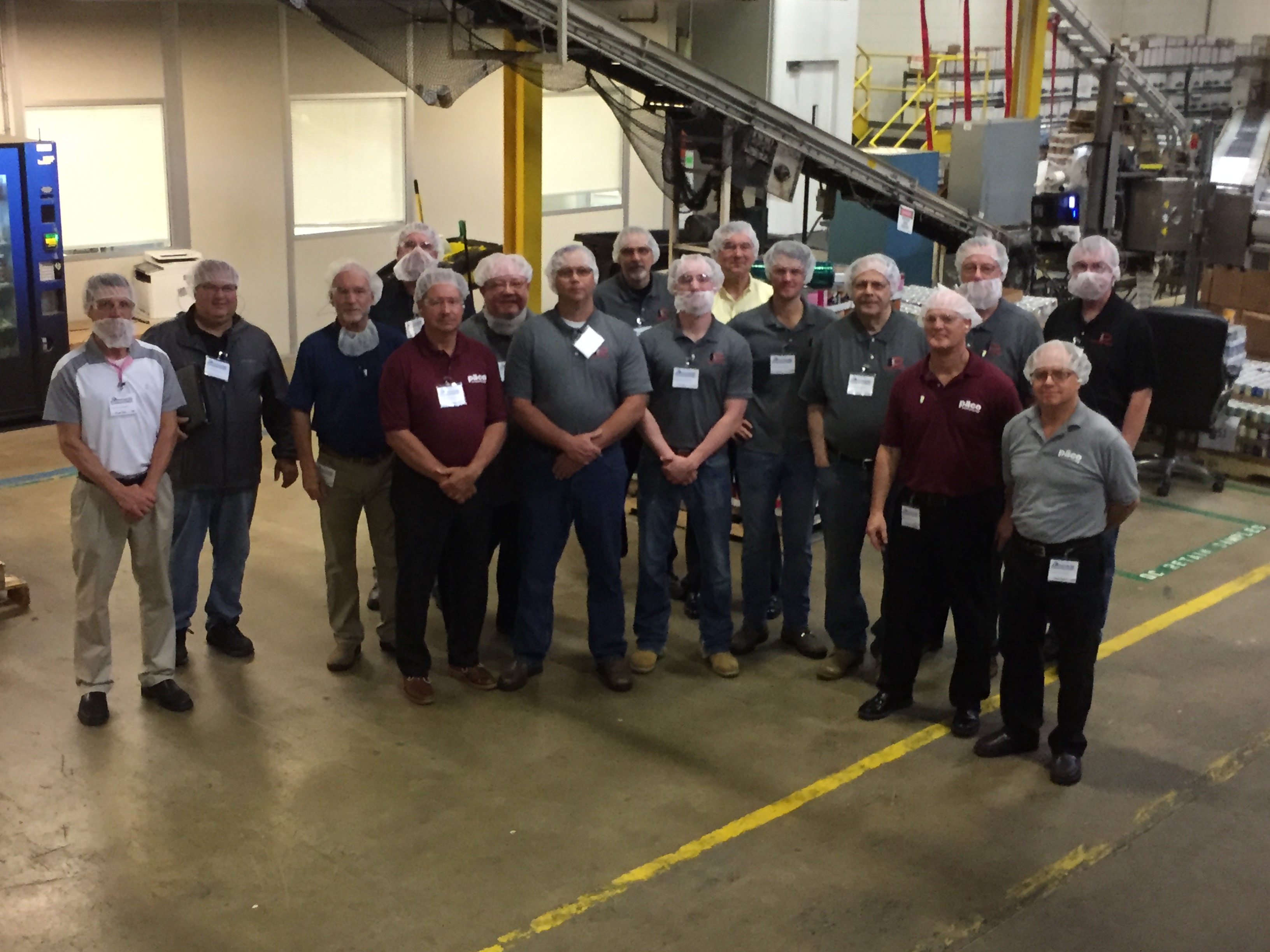
Conclusion
The third production line that our team provided has enabled Simmons to run 6- and 12-pack trays at higher speeds than previously capable. The project manager for Simmons throughout this endeavor was Bob Grazioli, who has positive things to say about the system. “It’s working well overall,” Bob commented after completion. “All of our needs were met, [the team] ran into some hiccups along the way but we tackled each of them, one at a time, until the punch list was complete.”
In the spring of 2018 during Precision Automation’s Joint Sales Meeting with the sales and management team of paco manufacturing, our group was treated to a tour of the Simmons’ plant and observed the system’s status in its semi-finished state, examining how the system’s operation would eventually increase the company’s overall capability.