Improving the Efficiency of CNC Machines
This blog was written & contributed by a guest blogger: Vincent Hua, Marketing Manager at TSINFA- more information about whom can be found at the bottom of the page. Although Precision Automation® is not strictly a machining shop, many of the principles discussed do apply for our CNC machining capabilities to help maximize our customers’ efficiency rates.
A machine shop wherein Computer Numerical Control (CNC) machining is carried out houses all the tools and machinery needed to make CNC parts, serving as a subtractive manufacturing environment. Advanced machines are known for their intricate products and components they develop, which have many moving parts and necessitate synchronized operation to operate at peak performance.
As a result, maintaining consistent manufacturing productivity levels reduces operating expenses and improves operational effectiveness. But how does a machining company achieve the best efficiency characteristics for a CNC machine shop? Here is a comprehensive guide that covers proven, actionable tips that can be implemented to achieve efficiency optimization in CNC machines.
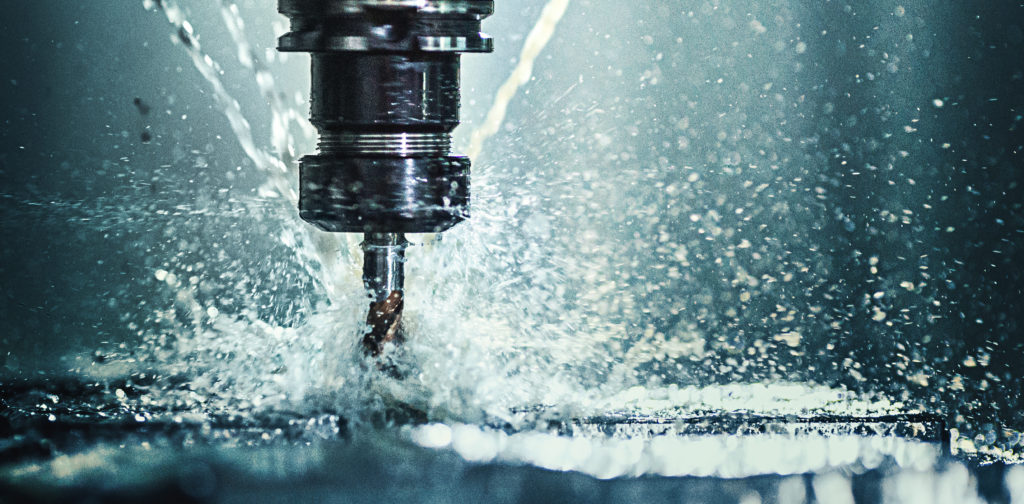
1. Investment in Manufacturing Technology Upgradation
Innovations in the way CNC machines function are largely influenced by manufacturing technology improvements. The majority of product development processes can now be automated thanks to the widespread utilization of CNC equipment like CNC turning, lathe, milling, EDM (Electrical Discharge Machining), etc. Machine operators can also easily navigate the manual and automated machinery in such workshops.
Therefore, one must employ cutting-edge technologies and machinery to manufacture CNC components rapidly and accurately. Plus, high-tech, custom-built machinery contributes to the highest possible productivity.
Initial purchasing of these types of cutting-edge equipment may be expensive, but it will pay dividends in the long run. Constant improvements to machinery are also necessary to maintain the firm’s competitive edge in the emerging sector.
2. Workflow Management Comes in Handy
Improving day-to-day operations is possible by analyzing and adjusting the workflow process. Loss of production time and lower productivity are the results of a poorly structured production floor.
Hence, workstations should be arranged and spaced out by typical daily operations. Operators should have easy access to the machinery, equipment, and tools they need to do their jobs effectively and efficiently. Consider reorganizing and implementing an integrative floor management system in the shop if the current arrangement is causing avoidable delays or unnecessary complexity.
Simplifying processes and increasing output is easy with lean material management. Although the lean manufacturing methodology was developed with industries in consideration, its underlying fundamentals apply to CNC machine shops of all capacities.

3. Plan out for Machinery Maintenance
Advanced machine shops require regular upkeep, just like the daily machinery they use. Preventive maintenance is a strategy for extending the serviceability and lifespan of the machinery and minimizing the likelihood of breaking down.
Modern machines are so advanced that they can even self-diagnose. These tools may power down automatically in precarious settings, minimizing the possibility of injury to workers or expensive equipment damage. While this could reduce the need for full-time shop repair & maintenance personnel, operators will still be required to undertake routine checks and carry out any necessary repairs.
4. Training Employees & Machinists is Vital
Clients tend to prefer to do business with a machine shop upon which they can rely. In addition to the requisite tools and resources, staff members must possess extensive knowledge and expertise to carry out product development processes successfully. There are always new technologies and processes being developed in the manufacturing industry, so it’s important to keep the staff up-to-date.
Experienced machinists are needed to operate each component of cutting-edge technology installed in the CNC machine shop. As a result, the corporation needs to provide ongoing training and undertake proficiency assessment tests for its workforce to ensure operators can manage every step of the manufacturing process.
There would be a significant reduction in time and expenses by deploying a skilled crew of machine operators that work together as a unit. They can manage various tasks and jobs with pinpoint accuracy and little blunders, increasing productivity and thus profits.
5. Ensure a Safer Manufacturing Environment
A well-performing machine shop will observe all necessary safety precautions and protocols. Ideally, machinery operators should be provided with a comforting and safe workspace in which to operate.
To run smoothly, a shop with CNC machines needs to have guidelines for employees to follow. Workers should always wear safety attire and protective gear throughout operations. To keep everyone safe, only trained machinists should manage the machinery.
The operators have the knowledge and abilities to run the necessary machinery, deal with potentially dangerous materials, and stock inventory properly. Furthermore, all-hazard symbols and exits from the work areas must be clearly labeled to ensure the safety of all employees.
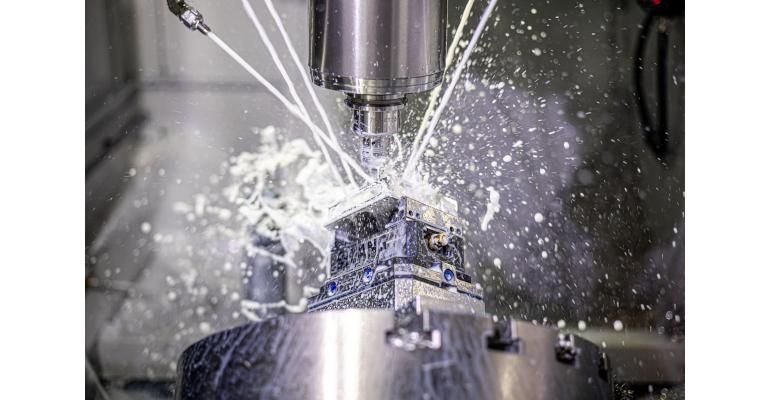
6. Keeping Expectations in Check
Last but not least, there should be reasonable expectations for the personnel. Long-term success requires a solid commitment to work as well as the ability to recognize when it’s time to call off for the day.
Similarly, workers cannot be asked to put in unnaturally long hours or sacrifice their free time to achieve the upcoming manufacturing deadlines. Keeping one’s expectations in check can lessen the likelihood that problems will arise as the business picks up.
Conclusion
The effectiveness of a company’s product development operations is crucial to stay competent amidst cut-throat competition. Only by establishing an efficient, tech-savvy, and organized CNC machine shop will manufacturers be able to keep up with the rising demand.
Thus, investing in cutting-edge technology and the employees and maintaining a streamlined workflow for personnel is crucial to the company’s long-term growth horizon.
About the Author: Vincent Hua is the Marketing Manager at TSINFA. He is passionate about helping people understand high-end and complex manufacturing processes. Besides writing and contributing his insights, Vincent is very keen on technological innovation that helps build highly precise and stable CNC Machinery.